How Palletizing With Proper Load Containment Reduces Stretch Film Usage
Equipment | Packaging Materials | Environment | The Business of Packaging | Technical Service and Support | Plant Performance | Shipping Protection | Food Packaging
Minimizing excess stretch film usage is important for reducing waste, saving money, and keeping your operation as efficient as possible. While stretch film is an invaluable product, the less you use while properly securing your loads, the better for your bottom line.
Load containment is one of the most important factors in this process. The term refers to the different forces that work in unison to hold your pallets together.
Proper load containment secures your product so it can travel and arrive intact. Here’s everything you need to know about making load containment your secret weapon:
Could automating your pallet wrapping save you money?
Check out our free Pallet Wrapper Investment Calculator!
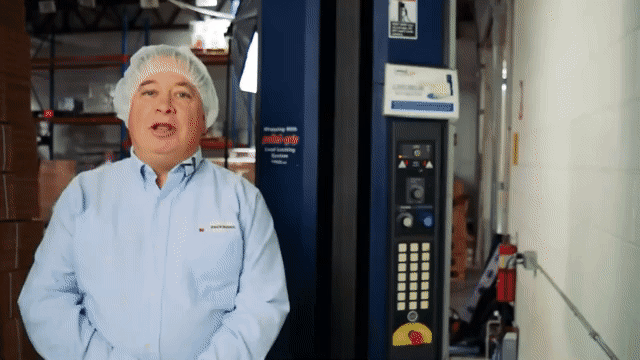
Types of Load Containment
So what does load containment refer to, exactly? The process includes three elements:
- The number of wraps or layers on your load.
- The wrapping force (i.e., how much force is applied via your stretch film).
- The gauge or thickness of your film.
All three of these are the secret sauce that keeps your pallet safe and secure.
There are multiple factors when it comes to ease of containment; primarily, length x width, and height. The larger the width x height, the easier the pallet to contain. With height, it can go either way — the height of the pallet can increase or decrease containment load depending on the weight and perimeter. And the ease of wrapping depends largely on how the pallet is packed.
There are three types of unitized loads, categorized by the types of items being shipped and how they reside on the pallet. These include:
- A-Profile Loads: These loads are uniform in shape and have no protrusions. They’re the easiest to wrap and often contain similar types of products loaded together.
- B-Profile Loads: These loads are less uniform, have puncture hazards fewer than three inches, and often have an irregular stacking pattern.
- C-Profile Loads: The most difficult type of load to wrap, these contain puncture hazards over three inches and typically consist of mixed products, often assembled at distribution centers for retail stores.
How Does Pallet Wrapping Work?
When it comes to pallet wrapping, specialized packaging machinery (a human) is usually the one doing the work. Manual wrapping is when employees wrap the plastic multiple times around a pallet. The problem here is that it’s far slower and a human only stretch the wrap at an average of 10% to 20%. Mechanized stretch wrapping can add a whopping 200% to 300% to the stretch length!
The mechanical pallet wrapping process involves assembling a load on a pallet, then stretch wrapping the entire package with a machine doing the labor. This insures consistent load containment so the products will arrive safely and securely at their destination while minimizing film usage and employee exertion.
Wrapping patterns are a key element when it comes to proper load containment. The patterns refer to where the film is placed on the load, and with mechanized wrapping, the specifications are programmed into the machine, i.e., how many wraps on the top of the load and how many on the bottom.
The fewer wraps necessary per load, the more savings your company sees. And that’s all about settings and calibration.
Pallet Wrapping Patterns
Most commonly, stretch wrapping begins at the bottom and works its way to the top, slightly overlapping with each wrap of film. Once the top layers are in place, the stretch wrapper will spiral wrap the full load until it gets to the bottom.
Overlapping is crucial, as it increases the strength of the bonding of each layer of stretch film in the center of the load.
Containment Force Vs. Film Force
Containment force is based on the weight of your contents.
Every additional layer added to the pallet increases the overall film force (also referred to as the “benefit per layer").
If your boxes are packed with potato chips or bubble wrap, for example, you’re looking at around two to five pounds of wrapping force.
For items such as cardboard boxes, the machine uses seven to 10 pounds of force. Heavier items like concrete or brick would have around 12 to 15 pounds of wrapping force.
Film force to load, another important measure, is how tight the film is being pulled as it exits the carriage and is applied to the load.
Pre-Stretching Rolls Saves Money
By lengthening film through a pre-stretch system, you can reduce costs by up to 50% and cut significantly back on how much stretch film you’re using. That’s better for the environment and your bottom line.
The more the film is stretched, the lower the usage and the greater the savings.
Pre-stretching is a process by which two rollers in your film delivery system turn at two different speeds, causing the film to elongate film and increase yield.
An average customer wrapping 50 loads (who has switched from hand wrapping or a machine without pre-stretch) can save around $50,000 in film over a decade.
Cautions to Be Aware Of
While the process of wrapping pallets and load containment concerns are key issues, the biggest factor in the supply chain tends to be the travel experience of the load itself. That’s where things tend to break down. Its important to secure your load for a harsh, bumpy road to its destination.
But saving money and becoming a more conscious company means working to lower the social, environmental and economic impacts of your packaging as it makes its way to its destination.
When you wrap your pallet and load together, there’s always a risk of punctures from forklifts or pallet jacks while moving them around which can reduce the containment force — so that’s always something to keep an eye on.
In addition, it’s important to consider transportation methods and storage placement so as to best minimize punctures, damage, sticking or improper wrapping that leads items to fall out. Safer is better!
Reusable Load Containment Is a New Trend
While stretch wrap is the easiest and most accessible option currently, reusable pallet wrapper materials are starting to make it to market.
The Envirowrapper, for example, is a reusable product designed to maximize pallet height while eliminating damage from loads falling over.
Another option is Gaprie’s P.C. Nets, a reusable load containment arena. Instead of a pallet wrap, it uses a net and cambuckle system. The net is pulled down over the pallet, keeping it secure.
Better Load Containment Can Boost Your Bottom Line
Load containment is a significant element when it comes to how efficient, safe, and affordable your shipping methodology is.
When done correctly, pallet wrapping can save you a significant amount of time, product damage reduction, and utilization of stretch film.
If you’re not sure how your system holds up, IP experts can do an audit or evaluation and make sure your current load containment scenario is optimal to keep your products safe as they travel.
Could an automated pallet wrapper be right for your business? See what the investment could save you and how long it could pay itself off with this handy Stretch Wrapper Investment Calculator!
About David Roberge
I am grateful for my 9 years as part of the outstanding Industrial Packaging team. I was able to hang out with some of the most knowledgeable folks in the packaging industry. I feel even luckier that I was able to share that knowledge with you. I love learning, hiking, and growing people and teams both personally and professionally, and helping companies grow better.